PROJECT MEMBER
-
古田 尚也
NAOYA FURUTA
生産本部 出雲工場
第二製造部 -
高橋 朗
AKIRA TAKAHASHI
生産本部 出雲工場
第三製造部 -
小平 和季
WAKI KOHIRA
生産本部 出雲工場
FAシステム課
自働化の基盤を築き、
人の可能性を引き出す
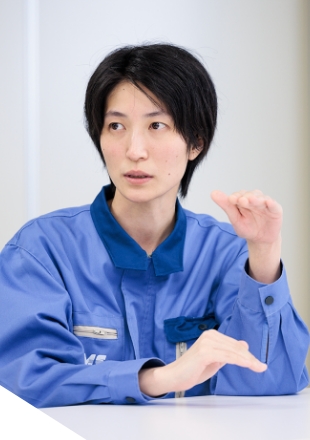
JMSでは、生産性の向上や品質の安定、原価低減を実現するために、製造工程における“自働化”を積極的に推進してきた。自働化とは、生産数や品質の管理に加えて稼働状態の監視など、人の働きを機械化することである。
JMSのマザー工場である出雲工場の第二製造部では、JMSの主力製品である輸液・輸血関連や経腸栄養関連の製品の組み立てを行っており、日々、少なくても数百、多くて数万の単位でさまざまな製品をつくっている。そのため、供給量の維持や人件費の削減など総合的な観点から、自働化を推進するという考え方があたりまえになっていた。その一環として、組み立てをする製品の切り替え時間を短縮させるために、工具の交換や材料の入れ替えなどをロボットで行う仕組みを整えた。人件費を削減することで原価低減を実現でき、さらに、人的ミスが起こらないなど、自働化を推進するメリットは多く、続々と展開させてきた。
第二製造部の古田も先人たちが取り組んできた自働化の設備について学びながら、より安く、そして品質の高い製品を医療現場に届けるために、新たな仕組みを取り入れた。設備に人の手が加わる頻度が多いとミスをする確率が上がるため、人の介入を最小限に抑えることが品質を保つ要因となると考えた古田は、人的ミスを抑えるために、設備にボタン一つで複数の変更を自働で行う機能を持たせたのだ。
しかし、ノウハウや技術は着実に蓄積されていても、部品の形状が複雑だったり、部品数が多かったりすると、自働化へ移行することが難しい製品がある。原価を低減させる企業努力も重要であるが、それ以上にJMSが重視しなければならないのは“品質へのこだわり”だ。いくら安く製品をつくり上げることができたとしても、品質異常を起こしてしまっては、何の意味もなさない。
作業者が行う工程の大切さを理解している古田は、作業者とロボットの工程を組み合わせた半自働化や、ロボットを導入せずにすべて作業者で行うという判断もしてきた。
古田の理想は保守・点検だけを作業者が行うという製造現場である。しかし、品質を守るという視点に立つと、自働化にも限界がある。そこで、古田は、現在、1人の作業者が複数の工程を担当できる“多能工”を育てることで、生産性と品質の向上を目指している。
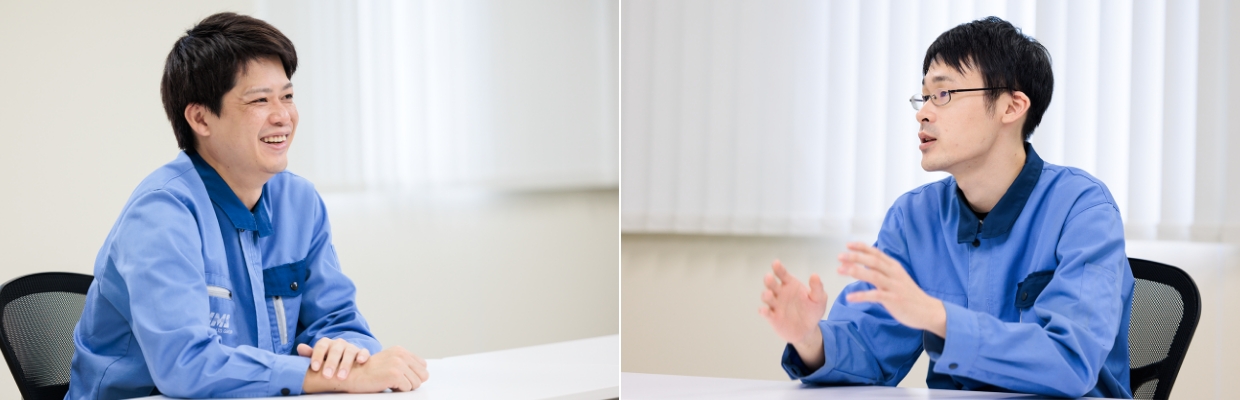
よりよい
ものづくりのために、
新たな領域へ挑戦する

一方、高橋が所属している第三製造部では、心臓外科手術において、患者様の心臓や肺の代わりに体外循環を行う人工心肺システムの製品の組み立てを行っている。この製品は病院ごとにカスタマイズしているので、1製品あたりの生産数がかなり少ない。さらに、形状が複雑な部品が多いため、組み立てには熟練した技術が必要とされる。そのため、自働化には不向きな製品とされており、作業者による組み立てがあたりまえとなっていた。
しかし、高橋は自働化を自部署でも取り入れ、品質改善や原価低減を目指していきたいという強い意志があった。なぜなら、これまで多くの時間をかけて教育し、一人前の基準を満たした作業者を育成しても、人によって組立作業時間にバラツキがあるという課題を抱えていたからだ。そのため、高橋は育成期間の短縮と製造工程の安定を実現するためには、自働化への挑戦が必要不可欠だと感じていた。
そこで、高橋は自働化を推進しているFAシステム課の小平に、「熟練の作業者の工程をロボットで再現できないだろうか」と相談することにした。
これまでいくつもの自働化を通じて、製造工程におけるコスト削減やスピードの向上、品質の安定などを実現してきた小平だったが、人工心肺システムの自働化は難しいと感じていた。しかし、JMS製品を必要としている医療現場の期待に応え続け、JMSのさらなる発展につなげるため、新領域に挑むことにした。
早速、小平は高橋から要望のあった、心臓手術の際に使用する心筋保護液などの薬剤を冷却加温する熱交換器の自働化に向けて、これまでのノウハウや経験を駆使して検討を始めた。しかし、ロボットの開発や導入コストに見合った実現可能なアイデアが浮かばず、頭を悩ませていた。「何かいい方法はないだろうか」と思い、情報収集するために参加したある展示会で、製造現場で応用できそうな『双腕ロボット』の存在を知った。それを見たとき、小平は人間と同じような動きができるのではないかと思った。そこで、目(カメラ)でモノの位置を確認する機能があるメーカーの双腕ロボットを借りて、使用する工具、材料の置く位置や並べ方を設計し、簡単な動きをさせてみる。ロボットの目の部分にセンサーがあることで、対象物のズレなどを検知し、動きを補正・調整しているロボットを見た小平は、今回の自働化に適したものだと確信し、本格導入することに決めた。
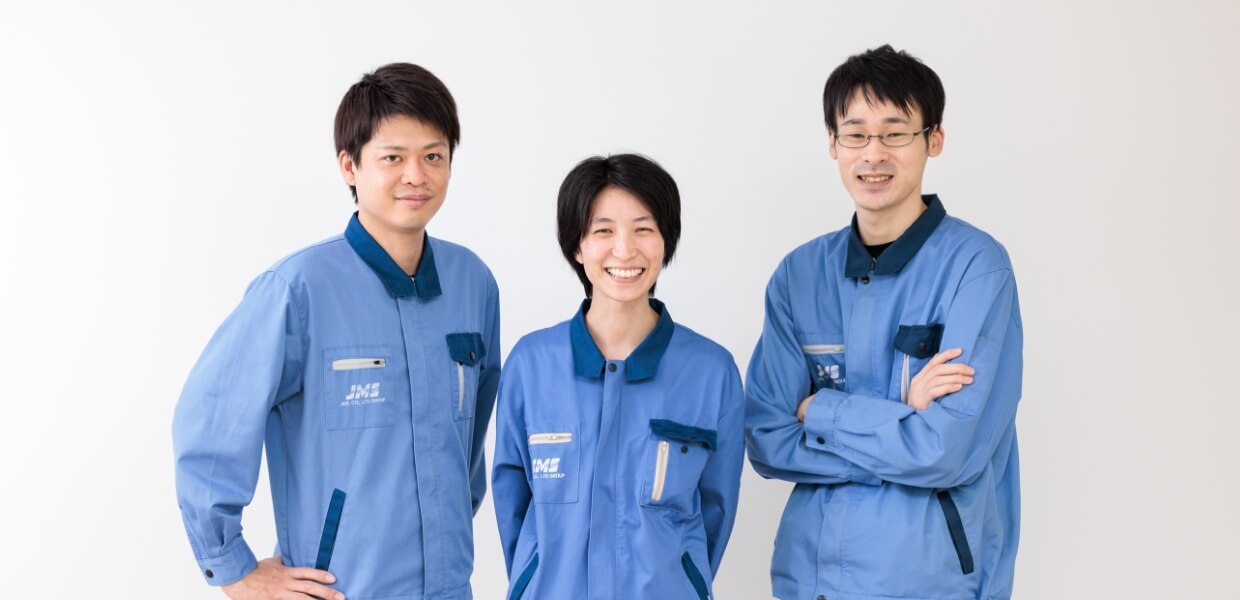
観察と創意工夫の先に
辿りついた、
自働化の可能性
高橋は小平から人間と近い動きをする双腕ロボットの説明を聞いたとき、自働化を実現できると期待に胸をふくらませた。しかし――小平がロボットの設計に着手すると、熟練の作業者の動きを再現することは簡単ではないことが分かった。人間に“近い”動きはできても、双腕ロボットに人間のような“繊細な”動きを再現させるのは不可能だったのだ。稼働域に制約があり、“できないこと”を理解したうえで、それを補うプロセスと設計が求められた。
小平がロボットの設計に落とし込めるよう、高橋は作業工程の現状分析をした結果を共有したり、作業者の様子を確認してもらい、作業のコツの説明を行ったりした。小平はロボットでできるようにするにはどうすればいいか考え、何度も何度も調整を行う。高橋はロボットを動かしたときに製造工程で起こった課題を小平に報告し、一緒に改善策を模索しながら、1年ほどかけて少しずつ解決しながら進めていく。
さらに、その試行錯誤の過程の中で、高橋と小平は作業時間の短縮も目指していた。小平は、すでに試作の段階で3時間かかっていたものを15分まで短縮させていたが、まだロボットの動きには改善の余地があったため、高橋と動きの効率化について協議することにした。工具の動かし方や作業の順番など小さな改善を積み重ね、9分まで短縮することができた。
しかし、最後の仕上げに近い工程で大きな壁にぶつかった。すべての鉄芯を挿入したあとに、プラスチックケースの端にある2枚のプレートを分離させて、反対側の端に動かしていくのだが、どうしてもプラスチックケースの内部でひっかかってしまい、移動できないのだ。
樹脂でできたプレートのサイズに若干の誤差があることが原因でひっかかってしまうということは分かっているのだが、それをどのようにすれば解消できるのかなかなか糸口がつかめない。熟練の作業者は手の力のかけ方を絶妙に工夫しながら、プレートを動かしているのだが、その繊細な動きは、とてもロボットには再現できないものだった。そのうえ、そのひっかかる事象が毎回発生するものではないということもさらに小平の頭を悩ませる。ひっかかるときの原因はどこにあるのか、それはなぜ発生するのか。小平は、熟練の作業者の動きを観察し、自身の手で作業をしたり、メーカーと協議したりして、解決方法を模索していく。そのなかでの小さな気づきをもとに、高橋と協力しながら創意工夫を施していく。小平と高橋の地道な努力によって、難所だった工程の問題も解決することができた。
そして、熟練者よりは遅いが、初心者よりも早い5分という作業時間で、熟練の技術が求められる工程の自働化をついに実現することができた。新たに開発された双腕ロボットは、出雲の地の縁から『スサノオ』と名付けた。スサノオの導入のおかげで、作業者への教育は機械のセットに関することだけになったため、育成期間の短縮と製造工程の安定という当初の目標を達成することができた。その後、他の部品の自働化も進み、いまではスサノオは1台で4部品の組み立てを担当している。
人工心肺システムの自働化は難しいと言われていた中、達成できたことは大きな自信になった、と高橋は振り返る。第二製造部では自働化を推進してきたが、製品の特性が異なるため、今回は新たな挑戦だった。そんな中でも実現できたのは、作業者との対話を重ね、声に耳を傾けられた結果と小平は話す。
今後、将来に向けて解決すべき課題は『人材不足』である。労働人口が減少し、人材の確保が難しくなっている現状であっても、JMSは安定的に高品質な製品を医療現場に届けるという使命がある。
そのために、貴重な人材を効率的に配置できるように、作業者が複数の工程に対応できる多能工の育成と自働化をさらに発展させていく必要があるが、単に自働化を推進するだけでは不十分だと、3人は考えている。なぜなら、多種多様な形状に応じて、個別にロボットが設計できても、投資に対する省人効果が得られにくく、費用対効果が見込めないからだ。そのため、今回、挑戦したスサノオのようなロボットの“多能工”も実現できる自働化を目指していく。これからも、JMSは、さらに難易度が高いと言われている工程における“多能工”と“自働化”へ挑戦をやめない。
POINT
- ・ロボットと作業者のそれぞれの特性を生かし、生産性の向上に取り組んでいる
- ・やるべきと思ったことは、難易度が高くでも挑戦できる風土がある
- ・互いに連携を取りながら、プロジェクトを成功させるために、努力を怠らない